Example : Supermarket Stock Control
Most businesses need to hold stocks of goods. Shops need to hold
stocks of goods they sell, and manufacturers need to hold stocks of raw materials and finished goods
they make. The task of recording and maintaining stock levels is called stock control.
A stock control system must keep an up-to-date record of all the
stock held and place orders for fresh deliveries if stock runs low. Large shops, supermarkets and
factories use computerised stock control systems.
Importance of stock control -
- adequate stocks must be maintained to supply a customer with goods
with minimum delay. If customers find goods are regularly out of stock they will go elsewhere.
- to keep business expenses to a minimum, goods must not be
overstocked. By keeping stocks to a minimum, a business can limit the amount of money invested in stock
and also reduce the risk of stock deteriorating before it can be sold. Minimum stock levels also
reduce storage costs such as warehousing, heating, lighting and security.
A real-time stock control system in a
supermarket :
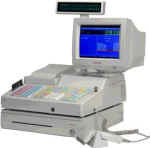 |
The POS
terminal only needs to pass the bar code on each item past a laser scanner. The scanner reads the code number stored in
the bar code and sends it directly to a computer. The computer checks the code and, if it is
valid, looks up the product's name and price in data files held on disc. The name and price
are sent back to the POS terminal. In this way the POS terminal can print out an itemised
receipt. |
Each terminal has a keyboard that can be used if a bar-code cannot be
read.
As each item is sold, the stock files are updated and orders are
printed when they become necessary.
- customer service is much quicker, reducing queues.
- few mistakes
in charging customers.
- prices can be changed easily.
- fully itemised bill can be provided for the customer.
- no staff needed for counting stock on shelves
BUT...
- the cost of the equipment is very high
- prices are usually only marked on shelves and not on individual
items. Customer confusion?
|